What’s the difference between supply chain vs logistics management, and why does it matter? These two terms are often used interchangeably, but they represent distinct functions within a company’s operations.
Understanding their differences is crucial for businesses that want to optimize efficiency, reduce costs, and enhance customer satisfaction.
Logistics management focuses on the movement, storage, and transportation of goods, ensuring that products get from one place to another efficiently.
On the other hand, supply chain management is a broader concept that encompasses everything from sourcing raw materials to delivering the final product to the customer.
Both play a crucial role in a company’s success, but failing to distinguish between them can lead to inefficiencies and missed opportunities.
In this blog, we’ll dive deep into supply chain vs logistics management, exploring their key differences, how they work together, and why understanding them is essential for improving business operations.
Table of Contents
Supply Chain vs Logistics Management: Understanding the 4 Key Differences
While supply chain management (SCM) and logistics management are closely linked, they serve distinct roles within a business’s operations.
Logistics focuses on the movement and storage of goods, while supply chain management takes a broader, more strategic approach, overseeing the entire flow of materials, products, and information from suppliers to customers.
Understanding these differences can help businesses improve efficiency, reduce costs, and enhance customer satisfaction.
1. Scope and Definition
Supply Chain Management (SCM):
SCM is a comprehensive, end-to-end process that involves sourcing raw materials, manufacturing, inventory management, order fulfillment, and customer service.
It encompasses multiple functions across various departments and organizations, aiming to optimize the entire production and distribution process.

Logistics Management:
Logistics is a subset of supply chain management that focuses specifically on the transportation, storage, and distribution of goods.
It ensures that materials and finished products are delivered efficiently, safely, and cost-effectively.
Logistics covers key activities such as warehousing, fleet management, freight transportation, and last-mile delivery.
Read more: Understanding the 6 Different Types of Supply Chain Management
2. Strategic vs Operational Focus
Supply Chain Management:
- SCM is strategic in nature, involving long-term planning to improve efficiency across the entire supply network.
- It deals with forecasting demand, supplier relationships, procurement strategies, and production planning.
- SCM focuses on cross-functional collaboration between procurement, production, sales, and logistics teams.
Logistics Management:
- Logistics is operational, concentrating on the daily execution of moving goods from one point to another.
- It ensures timely and cost-effective transportation, storage, and order fulfillment.
- Logistics managers focus on optimizing routes, managing carrier relationships, and reducing shipping costs.
Learn more on The Power of Global Sourcing in Supply Chain Management
3. Components and Functions
Aspect | Supply Chain Management | Logistics Management |
Scope | Broad, covering end-to-end processes from raw materials to final product delivery | Narrower, focusing only on transportation, warehousing, and distribution |
Focus | Strategic planning, demand forecasting, supplier management, cost reduction | Execution of transportation, warehousing, and order fulfillment |
Key Processes | Procurement, production, inventory control, demand forecasting, distribution | Warehousing, transportation, freight management, packaging, delivery |
Goal | Maximizing efficiency and reducing costs across the entire supply chain | Ensuring smooth, cost-effective movement and storage of goods |
Technology Used | Enterprise Resource Planning (ERP), Supply Chain Management Software | Transportation Management Systems (TMS), Warehouse Management Systems (WMS) |
For more information: The Positive and Negative Impacts of the Amazon Effect on Freight in Dubai
4. Role in Business Efficiency
How Supply Chain Management Contributes to Business Success
- Helps businesses source cost-effective suppliers and optimize production schedules.
- Improves inventory management, ensuring products are available without overstocking.
- Enhances customer satisfaction through efficient order fulfillment and supplier coordination.
- Reduces overall costs by streamlining procurement, production, and logistics.
How Logistics Management Enhances Operations
- Ensures timely delivery, reducing delays and improving customer service.
- Optimizes transportation costs by selecting efficient shipping methods.
- Manages warehouse operations to improve inventory accuracy and reduce waste.
- Enhances visibility and tracking of shipments to prevent disruptions.
For more information: Understanding the 6 Different Types of Supply Chain Management
The Relationship Between Supply Chain and Logistics
Logistics is an essential part of supply chain management, but the two are not the same. While supply chain management (SCM) oversees the entire journey of a product from raw material sourcing to final delivery, logistics focuses specifically on the movement, storage, and transportation of goods.
Think of SCM as the strategic backbone of a business’s operations, while logistics ensures that everything flows smoothly within that structure.
A well-functioning supply chain relies on efficient logistics, and logistics cannot operate effectively without a strong supply chain strategy. If one fails, the other suffers.
For instance, a well-planned supply chain without efficient logistics may lead to delayed shipments and dissatisfied customers, while excellent logistics without a coordinated supply chain can result in overstocked warehouses or stock shortages.
How Supply Chain and Logistics Work Together
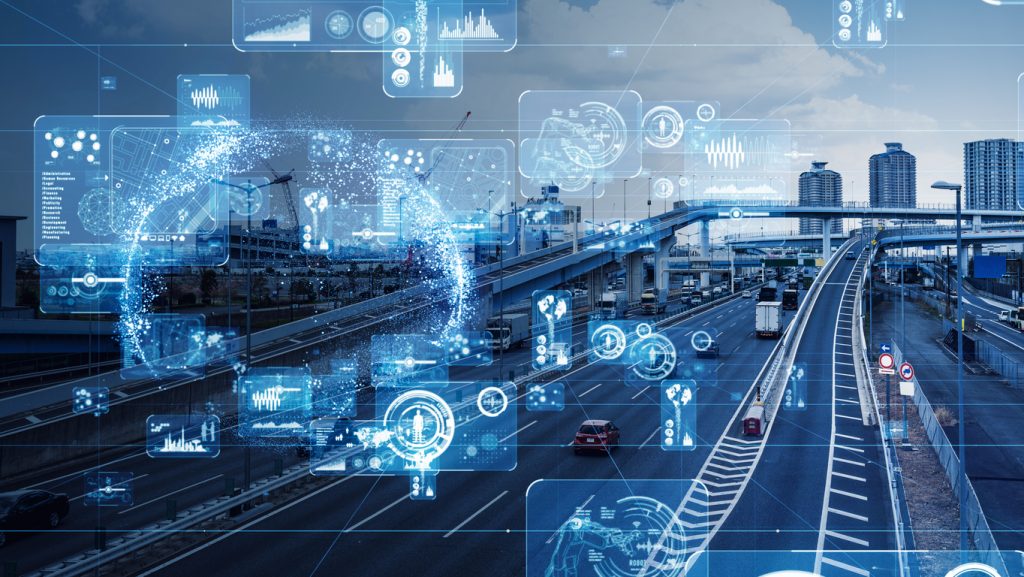
To better understand this relationship, consider a retail company preparing for the holiday season:
1- Supply Chain Management (SCM) Team:
- Analyzes historical sales data to predict demand.
- Communicates with suppliers to procure enough inventory.
- Ensures warehouses are stocked in advance to meet customer orders.
- Oversees production schedules to avoid shortages or overproduction.
2- Logistics Management Team:
- Coordinates transportation to ensure raw materials arrive at the factory on time.
- Manages warehousing and inventory placement for quick distribution.
- Oversees shipping and last-mile delivery to ensure products reach customers efficiently.
- Tracks shipments and resolves any transportation issues that arise.
Both teams must work in sync to prevent delays, avoid extra costs, and ensure smooth operations. If the SCM team fails to predict demand accurately, logistics may struggle with overstocked warehouses or empty shelves.
If the logistics team fails to deliver goods on time, the entire supply chain collapses, leading to customer dissatisfaction and lost revenue.
Read more: What is the Meaning of Stocktaking? The 4 Differences Between Stocktaking and Stock Checking
How Companies Use SCM and Logistics Differently
Consider a global e-commerce company like Amazon:
- Supply Chain Management: Amazon uses AI-driven demand forecasting, automated warehousing, and supplier coordination to ensure efficient product availability.
- Logistics Management: Amazon’s logistics network includes fulfillment centers, delivery partners, and last-mile delivery services to ensure fast shipping.
Both functions work together to deliver products quickly and efficiently to customers.
While Amazon prioritizes speed and scale, other companies tailor SCM and logistics to their specific needs. For example:
Walmart’s Supply Chain Management: Walmart’s strength lies in its vast, efficient distribution network, focusing on cost-effective bulk purchasing and streamlined inventory management.
They have a strong emphasis on supplier relationships, and using their scale to drive down cost. They are also utilizing more and more technology to streamline their supply chain.
Logistics Management: Walmart emphasizes a hub-and-spoke distribution model, utilizing a network of regional distribution centers to efficiently replenish its thousands of physical stores.
They are also expanding their e-commerce logistics, including curbside pickup and delivery services, with a focus on integrating physical and online channels.
They are working to optimize “first mile” pickup from vendors, to “last mile” delivery to the customer.
Walmart’s primary goal is to provide everyday low prices, which necessitates a highly cost-efficient supply chain and logistics operation. This differs from Amazon’s focus on speed and customer convenience.
Learn more: What are the 5 Components of a Supply Chain?
Concluding the supply chain vs logistics management debate
Understanding the differences between supply chain vs logistics management is essential for businesses looking to stay competitive in today’s fast-paced market.
While logistics management ensures goods are transported and stored efficiently, supply chain management takes a more comprehensive approach, overseeing the entire process from procurement to delivery.
When both functions are managed effectively, businesses can streamline operations, reduce costs, and improve customer satisfaction.
If you want to enhance your logistics operations and create a more efficient supply chain, Z Line Logistics is here to help.
Our expert team specializes in customized logistics solutions designed to meet your unique business needs. Contact Z Line Logistics today to discover how we can optimize your logistics strategy and keep your supply chain running smoothly!