Are you tired of excess inventory cluttering your warehouse and draining your resources? Discover the power of Just-in-Time (JIT) inventory management.
This lean manufacturing strategy can revolutionize your supply chain operations, helping you optimize efficiency, reduce costs, and improve customer satisfaction.
This comprehensive guide will delve into the intricacies of JIT, exploring its benefits, challenges, and best practices.
What is the JIT Inventory Method? A Definition
Imagine your kitchen stocked with ingredients for every meal you might ever cook. It’s a tempting idea, but it’s also inefficient and wasteful. That’s where Just-in-Time comes in.
JIT is a lean manufacturing strategy that’s like having a personal chef who shops for ingredients just before you need them.
By producing goods only when they’re needed, it minimizes inventory, reduces waste, and improves efficiency.
Think of it like this:
- No Overstocking: Instead of having a pantry overflowing with food you might never use, you only buy what you need for tonight’s dinner.
- Reduced Waste: You avoid throwing away food that’s gone bad because you bought it too early.
- Fresh Ingredients: You get the freshest ingredients because you’re buying them right when you need them.
JIT works the same way in manufacturing. By producing goods just in time for customer demand, businesses can reduce inventory costs, improve quality, and increase flexibility.
It’s a strategy that’s become synonymous with lean manufacturing and has been adopted by companies worldwide.
Learn more: The Positive and Negative Impacts of the Amazon Effect on Freight in Dubai
Key Principles of JIT Inventory Method
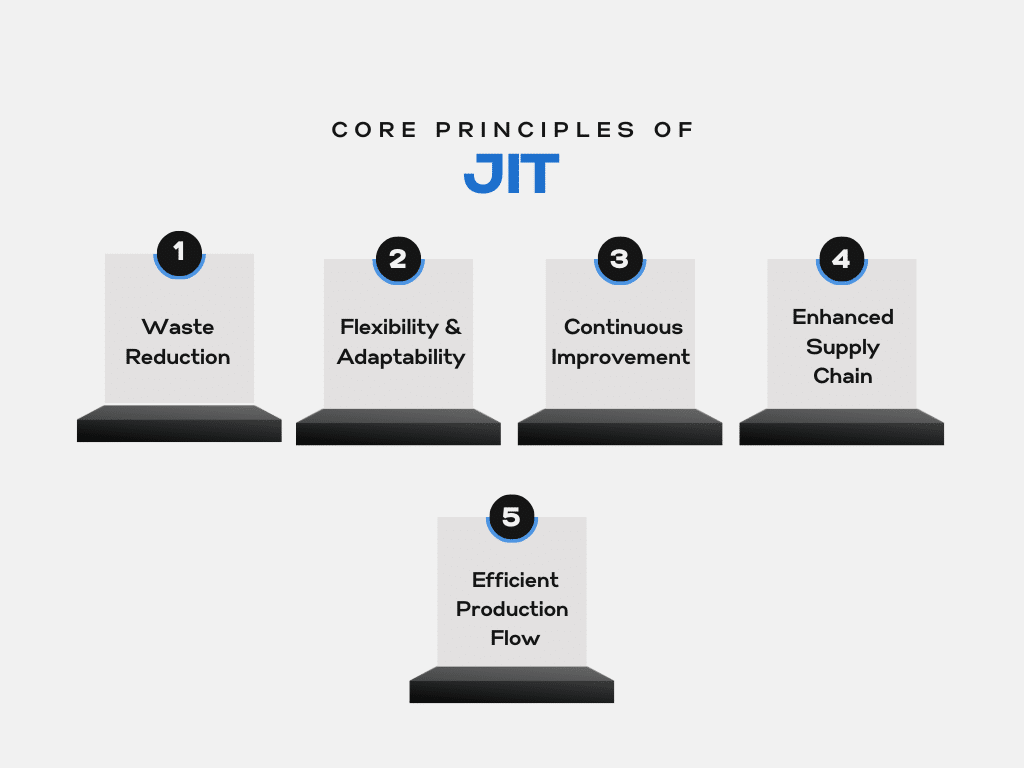
Just-in-Time is a lean manufacturing strategy that focuses on optimizing inventory and production processes. Here are the key principles that underpin it:
1. Minimal Inventory:
- Reduce Excess Stock: It aims to maintain only the necessary inventory to meet immediate production needs, minimizing storage costs and the risk of obsolescence.
- Just-in-Time Delivery: Suppliers deliver materials precisely when they are needed for production, eliminating the need for large stockpiles.
2. Continuous Flow:
- Eliminate Waste: It seeks to eliminate waste in all forms, including waiting time, transportation, overproduction, and defects.
- Smooth Flow: Ensure a continuous and uninterrupted flow of materials and products through the production process.
3. Pull System:
- Demand-Driven Production: Production is triggered by actual demand, rather than a predetermined schedule.
- Kanban: A visual signaling system often used in JIT to manage workflow and inventory levels.
4. Supplier Partnerships:
- Collaborative Relationships: Build strong partnerships with suppliers to ensure reliable delivery, quality materials, and continuous improvement.
- Shared Goals: Align supplier goals with your own to create a mutually beneficial relationship.
5. Quality Focus:
- Zero Defects: Strive for perfection in quality to avoid rework and waste.
- Continuous Improvement: Implement quality control measures and continuously seek ways to improve product quality.
For more information: Embracing Green Last-mile Delivery in Dubai for 2024
Benefits of JIT Inventory Method
By effectively implementing JIT, businesses can optimize their supply chain operations, reduce costs, improve quality, and gain a competitive edge in today’s market.
- Minimized Storage Costs: Smaller inventory means lower storage costs.
- Lower Insurance Premiums: Less inventory reduces insurance risks.
- Reduced Obsolescence Risk: Fewer products become outdated.
- Streamlined Production: It eliminates waste and improves productivity.
- Reduced Lead Times: Faster response to customer orders.
- Enhanced Quality: Focus on quality to avoid disruptions.
- Adaptability: Responds to market changes more quickly.
- Reduced Risk: Minimizes losses due to product changes or downturns.
- Efficiency: Operates more efficiently than competitors.
- Improved Customer Service: Faster delivery and higher customer satisfaction.
Learn mor: What are the 4 Pillars of Global Sourcing?
Disadvantages of Just-in-Time (JIT) Inventory Management
While JIT offers numerous benefits, it also presents some challenges and potential drawbacks. Here are some of the key disadvantages to consider:
- Reliability: JIT relies heavily on reliable suppliers who can deliver materials on time and in the required quantities. Disruptions in the supply chain can have a significant impact on production.
- Risk of Stockouts: If suppliers fail to deliver materials as scheduled, it can lead to stockouts and production delays.
- Natural Disasters: Natural disasters, such as earthquakes or hurricanes, can disrupt supply chains and impact JIT systems.
- Economic Downturns: Economic downturns can lead to decreased demand and excess inventory, making it difficult to maintain JIT principles.
- Unexpected Events: Unforeseen events, such as labor strikes or transportation issues, can disrupt the flow of materials and products.
- Complexity: Implementing JIT requires careful planning, coordination, and effective communication between suppliers, manufacturers, and logistics providers.
- Risk of Errors: Mistakes in forecasting demand or scheduling production can lead to disruptions and inefficiencies.
Learn more: What is Stock Inspection? Your 2024 Guide to Efficient Stock Inspection
JIT example: “A Case Study” Toyota’s JIT Experience
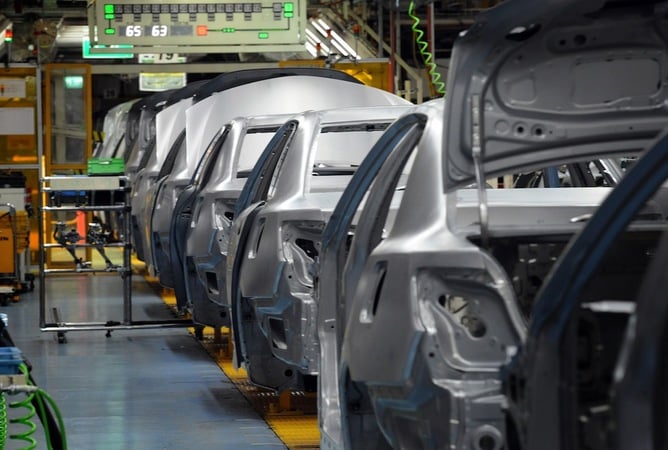
Toyota Motor Corporation, a pioneer of JIT, famously orders parts only when it receives new car orders. This approach has helped them streamline production and reduce costs.
However, even the best systems can face challenges. In 1997, a fire at a key supplier caused a temporary shutdown of Toyota’s production due to a lack of essential parts.
This incident highlighted the potential risks of relying solely on JIT, especially when dealing with single-source suppliers.
Lessons Learned from the COVID-19 Pandemic:
The COVID-19 pandemic further underscored the importance of supply chain resilience. Disruptions in global supply chains led to shortages of essential goods, highlighting the need for contingency plans and diversified sourcing strategies.
Read mor: Exploring Global Sourcing Advantages and Disadvantages
Mastering JIT: A Path to Supply Chain Excellence
By understanding and implementing JIT principles, you can unlock the full potential of your supply chain.
JIT offers a strategic advantage by minimizing waste, optimizing inventory levels, and improving overall efficiency.
Embrace the lean approach and experience the transformative power of JIT in your business with our experts at Z Line Logistics Company and advance your game.